What is Lancashire boiler?
Table of Contents
The Lancashire boiler is a type of steam boiler that was developed in the early 19th century in Lancashire, England. It was designed to handle high pressure and high steam capacity, making it ideal for use in large factories and mills.
The Lancashire boiler consists of two large cylindrical shells, one above the other. The upper shell is called the steam dome and contains the steam, while the lower shell contains the water. The two shells are connected by a number of fire tubes, which run through the water and are heated by hot gases from the furnace.
The furnace is located at one end of the boiler and is fired by coal or other fuel. The hot gases produced by the combustion of the fuel travel through the fire tubes, heating the water and producing steam. The steam is collected in the steam dome and then passed through a series of pipes to the point of use.
One of the main advantages of the Lancashire boiler is its large heating surface area, which allows for efficient heat transfer and high steam capacity. It is also relatively simple in design and easy to maintain, making it a popular choice for many industrial applications.
However, the Lancashire boiler has some disadvantages as well. It is relatively large and heavy, which can make it difficult to transport and install. It also requires a large amount of fuel to operate, which can be expensive. Despite these drawbacks, the Lancashire boiler remained a popular choice for many industrial applications throughout the 19th and early 20th centuries.
Diagram of Lancashire boiler
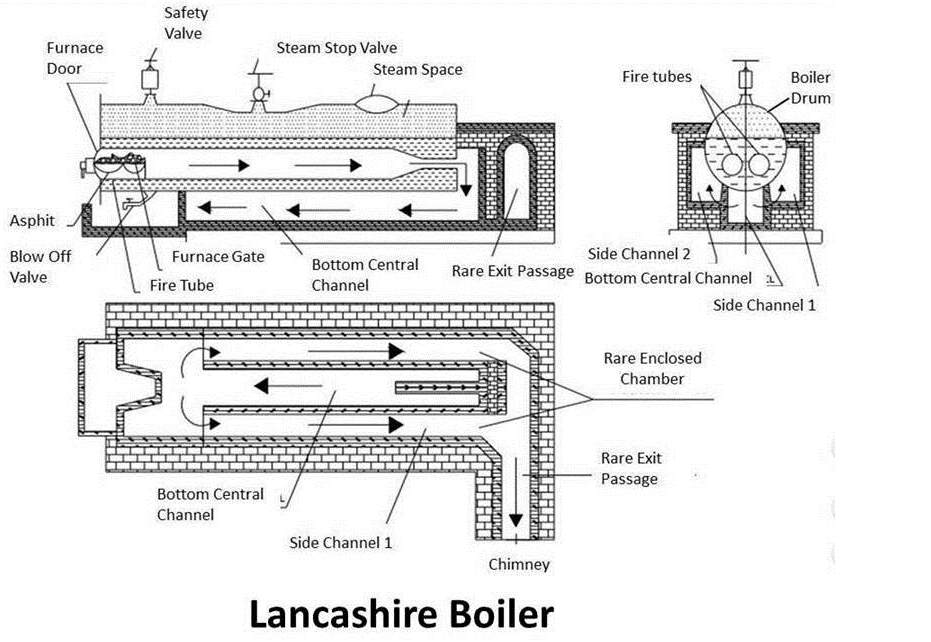
Parts and Construction of Lancashire boiler
The Lancashire boiler consists of two cylindrical shells, one above the other, with a central combustion chamber or furnace. The two shells are connected by a number of fire tubes that run through the water in the lower shell and are heated by hot gases from the furnace. Here are the main parts of a Lancashire boiler:
- Furnace: The furnace is the central combustion chamber of the boiler where fuel (coal, oil, or gas) is burned to produce hot gases. The furnace is typically located at one end of the boiler and is lined with firebricks to withstand high temperatures.
- Grate: The grate is a metal grid that supports the fuel in the furnace and allows air to flow through it for combustion.
- Combustion Chamber: The combustion chamber is the space above the grate where fuel is burned and hot gases are produced. The hot gases then flow through the fire tubes to heat the water in the lower shell.
- Fire Tubes: The fire tubes are a series of tubes that run through the water in the lower shell and are heated by hot gases from the combustion chamber. The hot gases pass through the fire tubes before being vented to the atmosphere through the chimney.
- Water Level Indicator: The water level indicator is a device used to monitor the water level in the boiler. It typically consists of a glass tube with markings that indicate the water level.
- Safety Valve: The safety valve is a critical safety feature of the boiler. It is designed to release steam if the pressure inside the boiler exceeds a safe level.
- Steam Outlet: The steam outlet is a pipe that carries the steam produced by the boiler to the point of use.
- Manhole: The manhole is an opening in the boiler that provides access for cleaning and maintenance.
The Lancashire boiler is typically made of high-quality steel and is designed to withstand high pressure and temperature. The boiler is typically mounted on a brick foundation and requires a chimney to vent the hot gases produced during combustion.
Working of Lancashire boiler?
The Lancashire boiler works by using heat from the combustion of fuel to heat water in the lower shell, producing steam that is collected in the upper shell and then delivered to the point of use. Here is a step-by-step explanation of how a Lancashire boiler works:
- Fuel is burned in the combustion chamber or furnace, producing hot gases.
- The hot gases flow through the fire tubes, which are surrounded by water in the lower shell of the boiler.
- Heat from the hot gases is transferred to the water in the fire tubes, causing the water to heat up and turn into steam.
- The steam rises to the upper shell, where it is collected in the steam dome.
- From the steam dome, the steam is delivered to the point of use through a series of pipes.
- As the steam is delivered, more water is added to the lower shell to replace the water that has been turned into steam.
- The pressure inside the boiler is controlled by a safety valve, which releases steam if the pressure inside the boiler exceeds a safe level.
- The hot gases produced during combustion are vented to the atmosphere through a chimney.
The Lancashire boiler is typically operated by a trained boiler operator who monitors the water level, pressure, and temperature inside the boiler to ensure that it is operating safely and efficiently. Regular maintenance and cleaning are also required to ensure that the boiler continues to operate properly.
Working principle of Lancashire boiler
The working principle of the Lancashire boiler is based on the transfer of heat from the combustion of fuel to the water in the lower shell of the boiler through a series of fire tubes. The hot gases produced during combustion pass through the fire tubes, transferring heat to the water and producing steam that is collected in the upper shell of the boiler. Here is a more detailed explanation of the working principle of the Lancashire boiler:
- Fuel (coal, oil, or gas) is burned in the combustion chamber or furnace, producing hot gases.
- The hot gases pass through the fire tubes, which are surrounded by water in the lower shell of the boiler.
- Heat from the hot gases is transferred to the water in the fire tubes, causing the water to heat up and turn into steam.
- The steam rises to the upper shell, where it is collected in the steam dome.
- From the steam dome, the steam is delivered to the point of use through a series of pipes.
- As the steam is delivered, more water is added to the lower shell to replace the water that has been turned into steam.
- The pressure inside the boiler is controlled by a safety valve, which releases steam if the pressure inside the boiler exceeds a safe level.
- The hot gases produced during combustion are vented to the atmosphere through a chimney.
The working principle of the Lancashire boiler is based on the transfer of heat from the hot gases produced during combustion to the water in the fire tubes. This allows for the production of steam that can be used to power a variety of industrial processes. The Lancashire boiler is a relatively simple and reliable design that has been used in a variety of industrial applications for over a century.
Application of Lancashire boiler
The Lancashire boiler was widely used in the 19th and early 20th centuries for a variety of industrial applications. Here are some of the main applications of the Lancashire boiler:
- Steam engines: The Lancashire boiler was commonly used to produce steam for powering steam engines, which were used to drive machinery in factories and mills.
- Textile industry: The Lancashire boiler was particularly well-suited for the textile industry, where it was used to power steam-driven looms and other machinery.
- Power generation: The Lancashire boiler was also used to produce steam for generating electricity in power plants.
- Food processing: The Lancashire boiler was used in food processing applications such as dairy and brewing industries, where steam was used to sterilize equipment and containers.
- Chemical industry: The Lancashire boiler was used in the chemical industry to produce steam for chemical reactions and other processes.
Today, the Lancashire boiler is less commonly used due to the availability of more efficient and advanced boiler designs. However, some Lancashire boilers can still be found in use in certain industries, particularly in developing countries where older technology is still in use. Additionally, the Lancashire boiler remains an important historical and technological landmark in the development of steam power and industrialisation.
Specification of Lancashire boiler
The specifications of a Lancashire boiler can vary depending on the manufacturer and the specific application, but here are some typical specifications for a medium-sized Lancashire boiler:
- Steam capacity: The steam capacity of a Lancashire boiler typically ranges from 9,000 to 34,000 kg/hr (20,000 to 75,000 lb/hr).
- Operating pressure: The operating pressure of a Lancashire boiler is typically 7-10 bar (100-150 psi).
- Efficiency: The efficiency of a Lancashire boiler is typically 60-80%, depending on the design and operating conditions.
- Fuel: Lancashire boilers can be fueled by coal, oil, or gas, although coal was the most common fuel used in the past.
- Shell diameter: The shell diameter of a Lancashire boiler is typically 1.8 to 2.7 meters (6 to 9 feet).
- Length: The length of a Lancashire boiler is typically 5.5 to 9 meters (18 to 30 feet).
- Number of fire tubes: A Lancashire boiler typically has two fire tubes that run the length of the boiler.
- Heating surface area: The heating surface area of a Lancashire boiler is typically 150-200 square meters (1,600-2,150 square feet).
- Weight: The weight of a Lancashire boiler can range from 25 to 50 tons, depending on the size and materials used.
It is important to note that these specifications are general guidelines and can vary depending on the specific design and application of the Lancashire boiler.
What are the advantages & disadvantages of Lancashire boiler?
Advantages of Lancashire boiler:
- Reliability: The Lancashire boiler is a simple and robust design that is known for its reliability and durability. It has been used for over a century in a variety of industrial applications, and its basic design has proven to be very reliable.
- Easy maintenance: The Lancashire boiler has a simple design that makes it easy to maintain and repair. Its cylindrical shape and simple construction make it easy to access the internal components, which reduces maintenance time and costs.
- High steam production: The Lancashire boiler is capable of producing large amounts of steam, making it well-suited for applications that require high steam production rates.
- Versatility: The Lancashire boiler can be fueled by a variety of different fuels, including coal, oil, and gas, which makes it a versatile choice for many different applications.
Disadvantages of Lancashire boiler:
- Slow steam production: The Lancashire boiler has a relatively slow steam production rate compared to some other boiler designs, which can limit its use in certain applications.
- Large size: The Lancashire boiler is a large and heavy design, which can make it difficult to transport and install in some locations.
- Low efficiency: The Lancashire boiler has a relatively low efficiency compared to some other boiler designs, which can result in higher fuel costs over time.
- Safety concerns: The Lancashire boiler requires careful monitoring and maintenance to ensure safe operation. In particular, the risk of explosion due to low water levels in the boiler can be a concern if proper safety precautions are not taken.
Overall, the Lancashire boiler has a number of advantages and disadvantages that should be considered when selecting a boiler for a particular application. While its reliability and versatility make it a popular choice for some applications, its slow steam production rate and low efficiency may limit its usefulness in others.
You may also read this –
FAQ’s
What are the 3 types of boilers?
There are many types of boilers, but here are three of the most common types:
1. Fire-tube boilers: In a fire-tube boiler, the hot gases from the combustion process pass through tubes that are surrounded by water. The heat is transferred to the water, which is heated and converted to steam. Fire-tube boilers are typically used for low to medium pressure applications and have a simple design.
2. Water-tube boilers: In a water-tube boiler, water flows through tubes that are surrounded by hot gases from the combustion process. The heat is transferred to the water, which is heated and converted to steam. Water-tube boilers are typically used for high-pressure applications and can have a more complex design than fire-tube boilers.
3. Electric boilers: Electric boilers use electricity to heat water or produce steam. They are often used in smaller applications or where there is no access to a gas supply. Electric boilers are typically more expensive to operate than boilers that use natural gas or oil, but they are more energy-efficient and may have lower maintenance costs.
Other types of boilers include combination boilers, which provide both heat and hot water, and condensing boilers, which are designed to capture and reuse heat from the combustion process for greater energy efficiency.
What type of boiler is Lancashire boiler?
The Lancashire boiler is a type of fire-tube boiler. In a Lancashire boiler, the hot gases from the combustion process pass through two large flues that run the length of the boiler, and the heat is transferred to the water that surrounds the flues. The water is then converted to steam, which is used for a variety of industrial applications. The Lancashire boiler is named after the county of Lancashire in England, where it was first developed in the mid-19th century.
Which fuel is used in Lancashire boiler?
The Lancashire boiler can be fueled by a variety of different fuels, including coal, wood, and oil. In modern applications, natural gas or propane is often used as the fuel source. The choice of fuel depends on a number of factors, including availability, cost, and environmental considerations. The Lancashire boiler’s simple and versatile design allows it to be adapted to a wide range of fuel sources, making it a popular choice for many different applications.
Why Lancashire boiler is low pressure boiler?
The Lancashire boiler is a low-pressure boiler because it is designed to operate at pressures of around 7 to 10 bar (100 to 150 psi). The boiler’s simple and robust design is well-suited to low-pressure applications, which typically require a large volume of steam at a relatively low pressure. The low pressure also helps to ensure safe operation of the boiler, as there is less risk of a catastrophic failure due to high pressure. Additionally, low-pressure steam is often used in industrial processes, such as heating and drying, that do not require high-pressure steam. Overall, the Lancashire boiler’s low-pressure design makes it a reliable and efficient choice for many different industrial applications.
What is the maximum pressure on a boiler?
The maximum pressure that a boiler can operate at depends on the design and construction of the boiler, as well as the intended application. Generally, industrial boilers are designed to operate at pressures ranging from 10 to 100 bar (145 to 1,450 psi), with some specialized boilers designed to operate at even higher pressures.
In the United States, the maximum allowable working pressure (MAWP) for a boiler is typically set by the American Society of Mechanical Engineers (ASME) Boiler and Pressure Vessel Code. The MAWP is the maximum pressure at which a boiler can operate safely and is determined based on the boiler’s design, construction, and testing.
It is important to note that operating a boiler above its rated pressure can be dangerous and can result in a catastrophic failure. Proper maintenance and regular inspections are essential to ensure safe and efficient operation of a boiler, regardless of its maximum allowable pressure.