Thermal equivalent stress is a term used to represent the combined effects of mechanical and thermal stresses on a material or structure. When subjected to elevated temperatures, materials undergo thermal expansion or contraction, which induces additional stresses. These thermal stresses can interact with existing mechanical stresses, potentially leading to accelerated material degradation or failure.
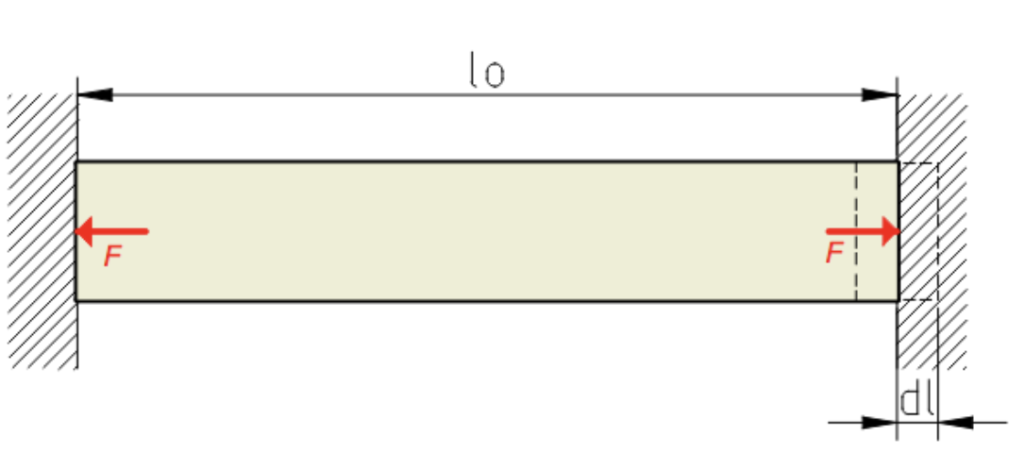
Significance in Structural Analysis:
Table of Contents
In many engineering applications, structures are exposed to temperature variations due to environmental factors or operational conditions. For example, components in aerospace, automotive, and industrial systems may experience significant temperature fluctuations during their lifecycle. Understanding the impact of these temperature changes is crucial for ensuring the structural integrity and reliability of the components.
Thermal Stress Components:
Thermal equivalent stress is composed of two main components: thermal stress and mechanical stress.
- Thermal Stress: This component arises from the expansion or contraction of a material due to temperature changes. As a material heats up, its molecules vibrate more vigorously, leading to an increase in volume. Conversely, cooling causes contraction. These thermal effects induce stresses within the material, and if not properly accounted for, can compromise the structural integrity.
- Mechanical Stress: Mechanical stress results from external forces applied to a structure, such as loads or pressure. When combined with thermal stress, mechanical stress can amplify or mitigate the overall stress experienced by the material.
Calculating Thermal Equivalent Stress:
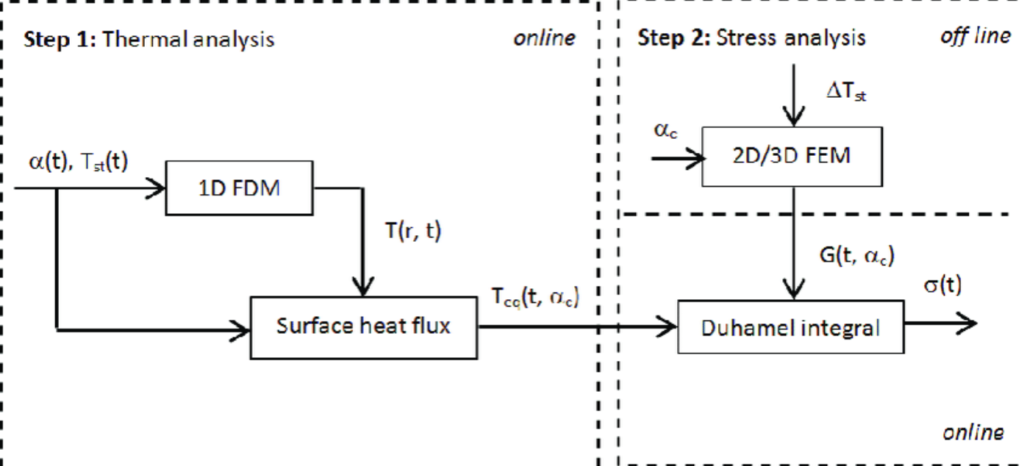
The calculation of thermal equivalent stress involves determining the combined effects of both thermal and mechanical stresses. Engineers use sophisticated mathematical models and finite element analysis (FEA) to simulate and predict how materials will behave under various temperature and loading conditions. This allows for the identification of potential weak points in a design and the optimization of materials to withstand challenging thermal environments.
How thermal equivalent stress is calculated
Let us consider that a solid rod with (A) area undergo thermal expansion. Original length L0 increase to L. The temperature rise is ^T.
L-L0= alpha ^t where alpha is the coefficient of material’s linear expansion.
L=L0 ( 1+ alpha ^t) So, thermal stress= F/A=Y( L-L0)/L0 where Y is Young’s modulus of a material.
Applications:
The understanding of thermal equivalent stress is critical in a wide range of industries, including aerospace, automotive, power generation, and manufacturing. For instance, in the aerospace sector, where materials are subjected to extreme temperature variations during flight, the accurate assessment of thermal equivalent stress is vital for ensuring the safety and longevity of components.
Thermal equivalent stress is a fundamental concept in structural analysis that bridges the gap between thermal and mechanical considerations. As industries continue to advance and push the limits of material performance, the ability to accurately predict and manage thermal stresses becomes increasingly essential. Engineers and designers must incorporate thermal equivalent stress analysis into their processes to create robust and reliable structures that can withstand the complex interplay of thermal and mechanical forces.